OIL, GAS, & CHEMICALS
CRUDE OIL BLENDING
Technics Inline Blenders can be adapted for use in crude oil applications and used to match your feedstocks to the needs of the downstream customer in order to enhance profitability and in some cases the usability of certain stocks
Technics Blenders can be Dual and Multi-Channel and optimized to prepare quality stocks that meet targets for Sulfur, Vapor Pressure, Acidity, Viscosity, Density, and Water Content.
These systems leave the Technics facility with the required valves, flow meters and other instruments pre-wired to the integral SCADA system with local operator interfaces. A computer and software package is provided for remote control, monitoring, and reporting. For Crude Oil and Heavy Fuel Oil applications, the system is often heat traced and insulated.
A typical process moves feedstocks through double block and bleed manual ball valves with each stream monitored for pressure. A coriolis meter provides volumetric and mass flow rate levels as well as a direct density measurement while flow control valves throttle the feed stocks proportionally to provide the proper blended product. Prior to injection in the blend header, actuated valves are used to isolate the channels.
The homogenization occurs in the blend header by use of a jet mixer which avoids the pressure loss encountered by the lower cost static mixer. However this mixing can sometimes be simple pipeline turbulence or by using in tank mixers.
Technics Blenders can be Dual and Multi-Channel and optimized to prepare quality stocks that meet targets for Sulfur, Vapor Pressure, Acidity, Viscosity, Density, and Water Content.
These systems leave the Technics facility with the required valves, flow meters and other instruments pre-wired to the integral SCADA system with local operator interfaces. A computer and software package is provided for remote control, monitoring, and reporting. For Crude Oil and Heavy Fuel Oil applications, the system is often heat traced and insulated.
A typical process moves feedstocks through double block and bleed manual ball valves with each stream monitored for pressure. A coriolis meter provides volumetric and mass flow rate levels as well as a direct density measurement while flow control valves throttle the feed stocks proportionally to provide the proper blended product. Prior to injection in the blend header, actuated valves are used to isolate the channels.
The homogenization occurs in the blend header by use of a jet mixer which avoids the pressure loss encountered by the lower cost static mixer. However this mixing can sometimes be simple pipeline turbulence or by using in tank mixers.
Blended Fuel for sampling exits a Swirl filter and is conditioned for pressure, temperature, and water content before entering the analyzers. These analyzer discharge the analyzed fuel into an atmospheric tank which automatically returns the waste fuel to the discharge header.
The key to a high performance Fuel Blending System resides in the analysis for such things as Sulfur, Vapor Pressure, Density, and Octane. Technics can adapt many combinations of analyzers to serve the need of the refinery. See our Online Analysis section for more information.
Critical to an effective blender is the control system.
These systems utilize Technics’ LOGOS as the software management and operator interface platform. A local HMI provides access to all of the systems parameters and has a graphical interface to the process. A SCADA system is included with a workstation, monitors and all peripherals.
LOGOS provides for precise blending and monitoring of any parameters available to the data acquisition system and the analyzers. The user can select a ratio control mode or an automatic update based on any of the measured variables. This feature adjusts the ratio of the feed streams such that the blend is optimized for Sulfur or Density or Viscosity as measured by the controller. In addition the LOGOS system typically has the following features
LOGOS provides for precise blending and monitoring of any parameters available to the data acquisition system and the analyzers. The user can select a ratio control mode or an automatic update based on any of the measured variables. This feature adjusts the ratio of the feed streams such that the blend is optimized for Sulfur or Density or Viscosity as measured by the controller. In addition the LOGOS system typically has the following features
- A graphical representation of the process
- Manual and Automatic Mode
- User Access control for Administrator, Supervisor, and Operator.
- Adjustable alarm levels for all parameters with date and time stamped alarm log.
- An event log to track changes to setpoints
- Full interface to the analyzers, and flow meters through Modbus digital communications eliminate resolution loss.
- A histogram recorder.
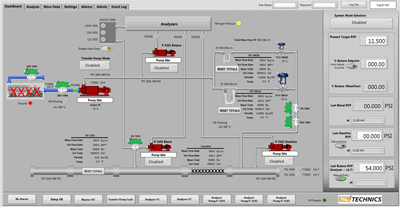
Process Screen
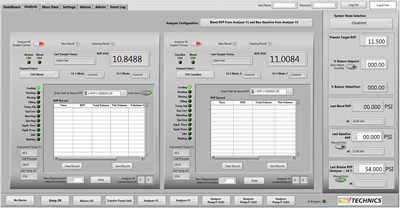
Analysis Screen